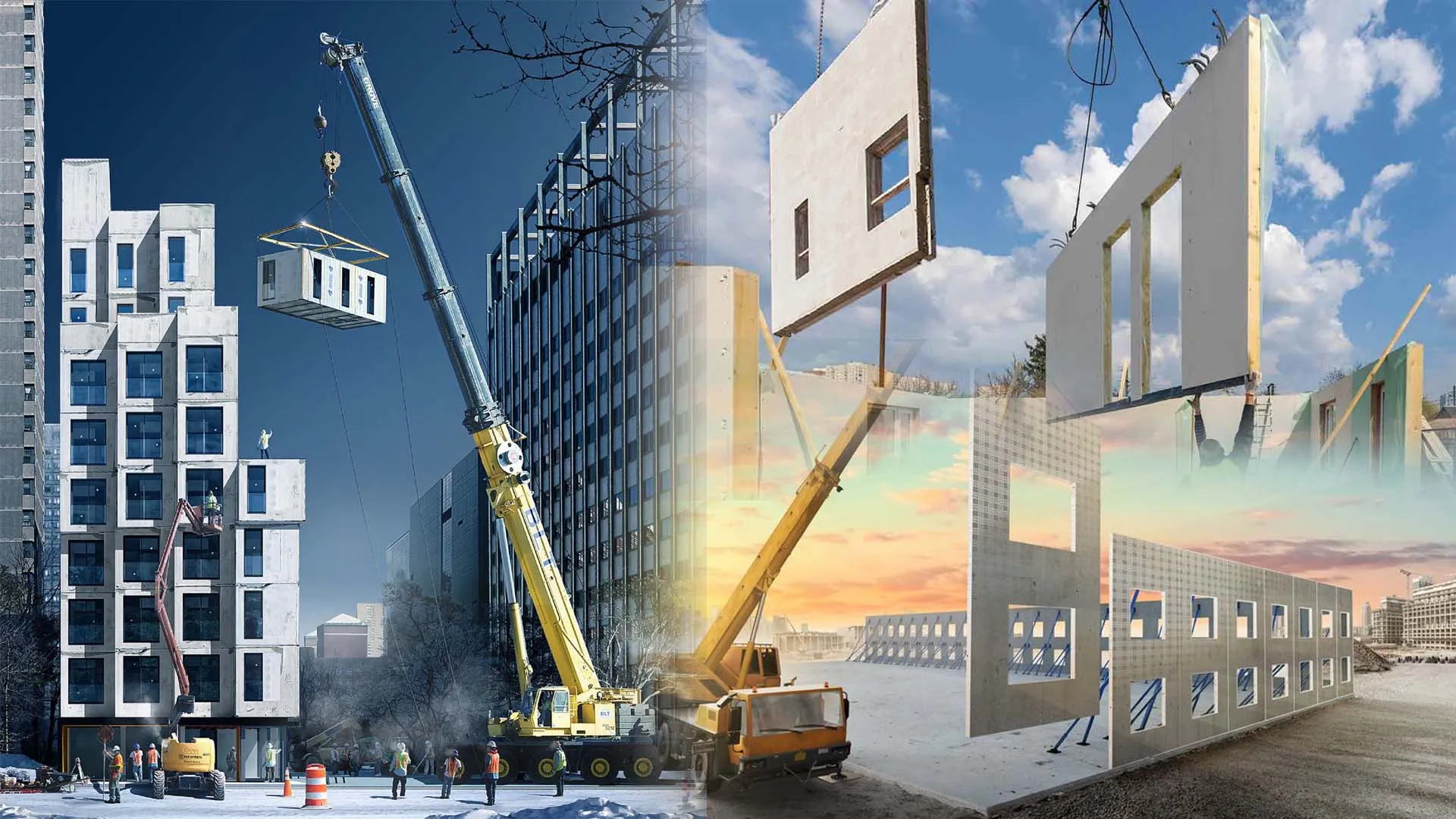
The Future of Prefabricated Buildings in Bangladesh
The Future of Prefabricated Buildings in Bangladesh
Md. Joynal Abdin*
Business Consultant & Digital Marketer
Founder & CEO of Trade & Investment Bangladesh
Design Possibilities:
- Customization: Prefabricated construction offers a high degree of customization. Architects can leverage computer-aided design (CAD) and parametric design tools to create unique, site-specific structures. This flexibility allows for the incorporation of complex geometries, varied building forms, and innovative architectural features.
- Material Innovation: Advances in materials have broadened the design possibilities for prefabricated buildings. The use of engineered wood products, such as cross-laminated timber (CLT), allows for the construction of tall and durable structures with a warm aesthetic. Additionally, sustainable materials like recycled steel and eco-friendly composites contribute to both design versatility and environmental responsibility.
- Integration of Technology: Prefabrication embraces the integration of smart technologies within building design. The incorporation of sensors, automation, and IoT devices enhances functionality and performance. For example, smart facades with dynamic shading systems respond to environmental conditions, improving energy efficiency and providing an interactive architectural element.
- Adaptive Reuse: Prefabricated construction lends itself well to adaptive reuse projects, allowing architects to repurpose existing structures or components. This sustainable approach enables the transformation of old buildings into modern, functional spaces while minimizing waste and preserving historical elements.
Architectural Flexibility:
- Modular Systems: Modular construction relies on the assembly of standardized units, providing architects with a modular system that allows for flexibility in design. These units can be combined in various configurations, creating diverse building layouts and forms. The modular approach is exemplified by projects like the Hivehaus in the United Kingdom, where hexagonal modules are arranged to form unique, interconnected living spaces.
- Stackable and Expandable Modules: Prefabricated buildings can be designed with stackable and expandable modules, allowing for vertical expansion or the addition of new modules over time. This adaptability is showcased in projects like the Box Office, a modular office building in Providence, USA, where shipping containers were stacked to create a dynamic and efficient workspace.
- Hybrid Construction: Architects are increasingly exploring hybrid construction methods that combine traditional and prefabricated elements. This approach allows for the incorporation of unique architectural features while harnessing the efficiency of prefabrication. The use of prefabricated components in conjunction with on-site construction techniques enables the realization of complex designs.
Case Studies Showcasing Innovative Prefab Structures:
- The Banyan Treehouse, Hawaii: This project demonstrates the integration of prefabricated components with the natural environment. Elevated on stilts, the treehouse consists of prefabricated modular sections that provide a luxurious, sustainable retreat in the midst of nature.
- The Broad Sustainable Building (BSB) Sky City, China: BSB Sky City holds the record for being one of the tallest prefabricated buildings globally. Its modular construction approach allowed for the rapid assembly of the 57-story tower, showcasing the scalability and efficiency of prefabrication.
- CopenHill, Denmark: CopenHill is a waste-to-energy plant that doubles as a recreational space. Its facade features prefabricated aluminum bricks, creating a visually striking and sustainable design that incorporates recreational facilities, a ski slope, and hiking trails.
Economic Benefits:
Prefabrication, also known as modular construction or off-site construction, offers notable advantages in terms of cost-effectiveness and efficiency. This construction method has the potential to significantly reduce construction time and labor costs, making it an appealing choice for various types of projects.
- Reduced Construction Time:
- Parallel Construction Phases: One of the key factors contributing to the reduced construction time in prefabrication is the ability to conduct multiple phases of the construction process simultaneously. While site preparation and foundation work are underway, the manufacturing of building components can occur off-site. This parallelization of tasks accelerates the overall construction timeline.
- Streamlined On-Site Assembly: Prefabricated components, being manufactured off-site, arrive at the construction site ready for assembly. This eliminates the need for extensive on-site fabrication, reducing the time required for traditional construction activities. Projects can be completed in a fraction of the time compared to conventional building methods.
- Predictable Construction Schedule: Prefabrication allows for greater control over the construction schedule. With components being manufactured in a controlled factory environment, the impact of weather conditions on construction timelines is minimized. This predictability in the schedule can be particularly advantageous for meeting tight deadlines.
- Labor Cost Savings:
- Efficient Resource Allocation: Prefabrication optimizes labor resources by shifting a significant portion of the construction work to the controlled environment of a factory. Skilled workers can focus on specialized tasks, such as precision manufacturing, while on-site labor is primarily dedicated to assembly. This efficient allocation of resources reduces labor costs.
- Reduced On-Site Labor Requirements: On-site construction involves a range of tasks, including cutting, shaping, and assembling building components. Prefabrication transfers these activities to the factory, minimizing the need for a large on-site workforce. This reduction in on-site labor requirements not only decreases costs but also addresses challenges associated with skilled labor shortages.
- Faster Assembly with Skilled Labor: The on-site assembly of prefabricated components is typically faster and requires a skilled workforce. With components designed for easy integration, skilled labor can efficiently carry out assembly tasks, further contributing to cost savings.
- Material Cost Optimization:
- Bulk Purchasing and Standardization: Prefabrication often involves bulk purchasing of materials and standardization of components. This can result in cost savings, as bulk orders often lead to discounted prices, and standardization streamlines the manufacturing process.
- Reduced Material Waste: The controlled environment of a factory allows for precise measurement and cutting of materials, minimizing waste. The reduction in material waste not only contributes to cost savings but also aligns with sustainable construction practices.
In conclusion, prefabrication offers a cost-effective and efficient alternative to traditional construction methods. The reduction in construction time, optimized labor utilization, and material cost savings make prefabrication an attractive option for various construction projects. As the industry continues to innovate, the cost-effectiveness and efficiency of prefabrication are likely to drive increased adoption across diverse sectors of the construction industry.
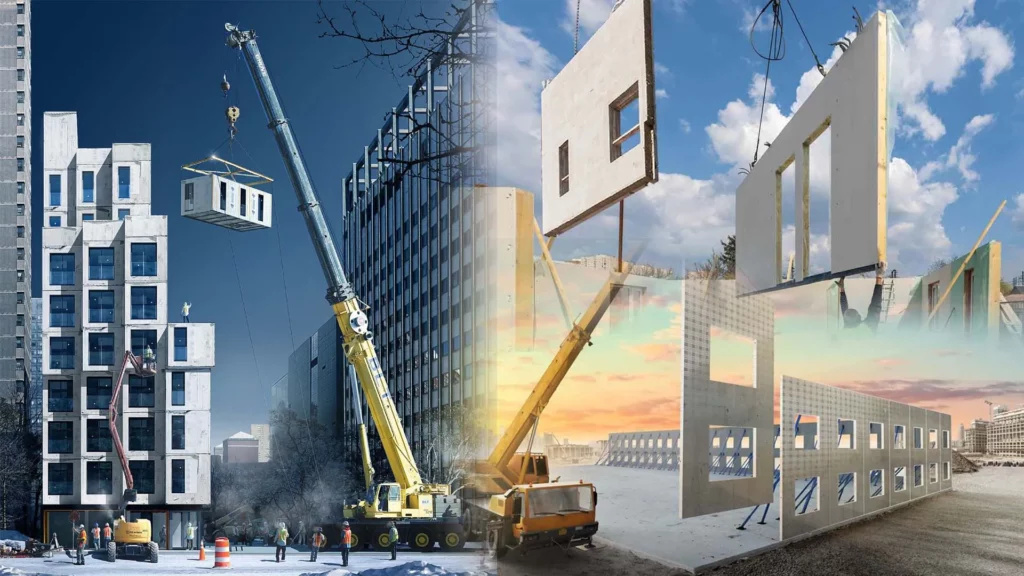
Environmental Sustainability:
Prefabricated construction, with its controlled manufacturing processes and emphasis on sustainability, presents several eco-friendly aspects that contribute to the reduction of waste and the overall carbon footprint compared to traditional construction methods. These environmentally conscious features make prefabrication an attractive option for those seeking sustainable building solutions.
- Precision Manufacturing and Reduced Waste:
- Efficient Material Usage: In prefabricated construction, materials are precisely cut and shaped in a controlled factory environment. This precision minimizes material waste, as components are manufactured to exact specifications, reducing the need for excess material that often occurs in traditional construction where cutting and shaping are done on-site.
- Optimized Material Selection: Prefabrication allows for the use of eco-friendly and sustainable materials. Builders can choose materials that have a lower environmental impact, such as recycled steel, engineered wood, or other sustainable composites. This conscious material selection contributes to reducing the overall environmental footprint of the construction process.
- Transportation Efficiency:
- Reduced Transportation Emissions: Prefabricated components are manufactured off-site and then transported to the construction site. While transportation does contribute to the carbon footprint, the overall emissions are often lower than in traditional construction. The efficiency of transporting standardized, pre-assembled components reduces the number of trips required compared to the transport of raw materials to a construction site.
- Localized Manufacturing: Prefabrication can involve setting up manufacturing facilities closer to the construction site, reducing the distance traveled during transportation. This localization further minimizes the environmental impact associated with the delivery of materials and components.
- Energy Efficiency and Sustainable Practices:
- Energy-Efficient Designs: Prefabricated buildings can be designed with a focus on energy efficiency, incorporating features such as better insulation, advanced ventilation systems, and energy-efficient windows. These design elements contribute to reduced energy consumption during the operational phase of the building.
- Renewable Energy Integration: Prefabricated construction allows for the integration of renewable energy technologies, such as solar panels, during the manufacturing process. This approach supports the use of clean energy sources, reducing the reliance on non-renewable energy and minimizing the carbon footprint associated with energy-intensive manufacturing processes.
- Reduced On-Site Disruption:
- Minimized Environmental Impact on Site: Prefabricated construction reduces the amount of on-site work required, resulting in less disruption to the surrounding environment. This is particularly relevant in urban areas where traditional construction methods may cause noise pollution, dust, and disturbance to local ecosystems.
- Faster Construction Times: The accelerated construction timeline associated with prefabrication means that on-site activities are completed more quickly. This not only reduces the duration of potential environmental disruption but also lessens the overall impact on local communities.
Challenges and Solutions:
Adopting prefabrication in Bangladesh, like in any other country, can face several challenges. However, with strategic planning and effective solutions, these obstacles can be overcome. Here are some common challenges and potential strategies to address them:
- Limited Awareness and Education:
Challenge: Lack of awareness and understanding of prefabrication methods.
Strategy: Conduct workshops, seminars, and training programs to educate architects, engineers, and construction professionals about the benefits and applications of prefabrication. Create awareness campaigns to inform the general public.
- Skilled Labor Shortage:
Challenge: Limited availability of skilled labor with expertise in prefabrication techniques.
Strategy: Invest in training programs to develop a skilled workforce. Collaborate with educational institutions to introduce courses on prefabrication. Import expertise or collaborate with international companies to transfer knowledge.
- Regulatory and Standards Compliance:
Challenge: Lack of specific regulations and standards for prefabricated construction.
Strategy: Work with regulatory bodies to develop and implement guidelines for prefabrication. Collaborate with international organizations to adopt best practices. Demonstrate the safety and quality standards of prefabricated structures through pilot projects.
- Supply Chain Issues:
Challenge: Inefficient supply chain management leading to delays and increased costs.
Strategy: Develop a robust supply chain with reliable suppliers. Foster partnerships with local manufacturers and suppliers. Implement advanced logistics and inventory management systems to streamline the supply chain.
- Perception and Cultural Acceptance:
Challenge: Resistance to change and traditional construction methods deeply ingrained in the culture.
Strategy: Engage in public relations and marketing efforts to change perceptions. Showcase successful prefabrication projects to build trust. Involve local communities in the planning process to address concerns and build acceptance.
- Infrastructure Challenges:
Challenge: Inadequate transportation and logistics infrastructure for prefabricated components.
Strategy: Collaborate with government agencies to improve transportation infrastructure. Plan prefabrication projects based on existing logistical capabilities. Explore modular construction methods that minimize transportation challenges.
- Cost Concerns:
Challenge: Perceived high initial costs associated with adopting prefabrication.
Strategy: Conduct a life-cycle cost analysis to demonstrate long-term savings. Implement pilot projects to showcase cost-effectiveness. Collaborate with financial institutions to develop financing options for prefabricated construction.
- Technology Integration:
Challenge: Limited access to advanced technology for prefabrication.
Strategy: Facilitate technology transfer through partnerships with international firms. Encourage research and development in local institutions. Provide incentives for the adoption of advanced construction technologies.
- Environmental Considerations:
Challenge: Lack of emphasis on sustainable and eco-friendly construction practices.
Strategy: Highlight the environmental benefits of prefabrication, such as reduced waste and energy efficiency. Align prefabrication projects with sustainability goals. Seek certification from relevant environmental standards.
- Collaboration and Communication:
Challenge: Inadequate collaboration and communication among stakeholders.
Strategy: Establish effective communication channels and collaboration platforms. Foster a culture of teamwork among architects, engineers, contractors, and suppliers. Use digital tools and project management systems to enhance collaboration.
By addressing these challenges with well-thought-out strategies, Bangladesh can successfully adopt and benefit from prefabrication in its construction industry. It’s essential to involve all stakeholders, including government bodies, industry professionals, and the public, in the process of promoting and implementing prefabrication techniques.
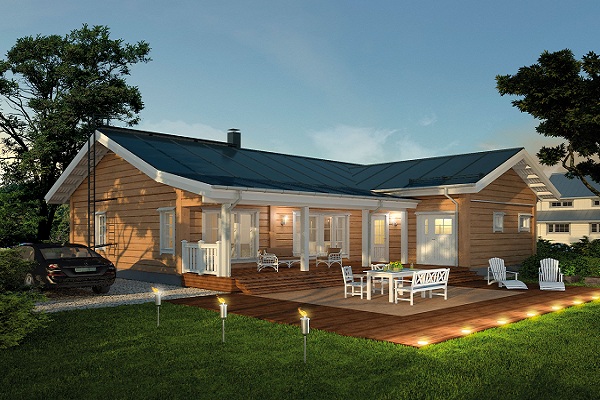
Closing Remarks:
In conclusion, the future of prefabricated buildings in Bangladesh holds immense promise for revolutionizing the construction landscape. Embracing prefabrication represents a pivotal step towards overcoming traditional challenges, ushering in an era of efficiency, sustainability, and economic viability.
As Bangladesh navigates the complexities of urbanization and infrastructure development, prefabrication emerges as a beacon of innovation. With the potential to address issues of skilled labor shortages, accelerate construction timelines, and enhance cost-effectiveness, prefabricated buildings align seamlessly with the nation’s aspirations for progress.
However, this transformative journey demands a collective commitment. It necessitates collaboration between public and private sectors, a concerted effort to educate and train a skilled workforce, and the establishment of regulatory frameworks that foster the integration of prefabrication. Moreover, cultural acceptance and awareness play integral roles in shaping the narrative around these modern construction methods.
As we look ahead, envisioning a skyline adorned with prefabricated structures, it is imperative to view challenges as opportunities for growth. The future of prefabricated buildings in Bangladesh hinges on adaptability, resilience, and a shared vision for a more sustainable and technologically advanced construction industry. By embracing this future, Bangladesh can not only meet the demands of its burgeoning population but also emerge as a global leader in innovative and forward-thinking construction practices. Together, let us build a future where prefabrication serves as a cornerstone for a more prosperous and resilient Bangladesh.
To read 1st part of this article, click here!
The Future of Prefabricated Buildings in Bangladesh: The Future of Prefabricated Buildings in Bangladesh
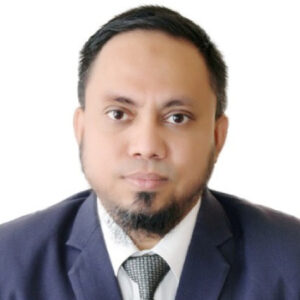
Mr. Md. Joynal Abdin stands as a prominent Business Consultant and Digital Marketer hailing from Dhaka, Bangladesh. He holds the role of Founder and CEO at Trade & Investment Bangladesh. With an extensive professional journey, he has contributed significantly, having served as Executive Secretary at Dhaka Chamber of Commerce & Industry (DCCI), Executive Director at DCCI Business Institute (DBI), Deputy Manager at SME Foundation, and Assistant Secretary at the Federation of Bangladesh Chambers of Commerce & Industry (FBCCI).
Mr. Abdin’s diverse array of services encompasses, but is not confined to, Business Research and Documentation, such as Feasibility Studies, Project Proposal Preparation, and Business Manual and Standard Operating Procedures writing. He is also adept at Export Market Selection, Product Positioning both domestically and internationally, Buyers-Sellers Matchmaking, Website Development, Search Engine Optimization (SEO), and Social Media Marketing, among other valuable offerings.